
Green steel from northern Sweden
Covered with buyer credit cover, contract bond cover, manufacturing risk cover and supplier credit cover
First large-scale green steelworks in Europe
Just a few kilometres south of the Arctic Circle in the Swedish region of Norrbotten, H2 Green Steel is building the world’s largest green steelworks. The Swedish start-up uses hydrogen, which it obtains from an electrolysis plant at the project site, to operate the exclusively electrically powered steelworks. The electricity required comes from hydroelectric and wind power. The plant is scheduled to go into operation at the end of 2025 and will produce 5 million tonnes of almost carbon-free steel per year from 2030.
With this project, the company aims to accelerate change in the industry by eliminating almost all carbon emissions from the steel production process. Conventional steelworks are responsible for around seven per cent of global carbon emissions. Accounting for around 30% of industrial emissions, the steel industry generates the largest proportion of greenhouse gas emissions in industry.
Electricity from renewable sources
The location in northern Sweden for the project was selected primarily due to the high availability of electricity from renewable sources. The simultaneously low electricity costs represent a decisive competitive advantage for energy-intensive steel production. Another advantage is the proximity to iron ore deposits and the availability of scrap iron.
The project site, which is located to the east of the small town of Boden, is well connected logistically to the industrial harbour in Luleå, around 30 km away, via a rail link.
One of the largest electrolysis plants in Europe
The steelworks will consist of an electrolysis plant, a direct reduced iron plant and a mini-mill flat steel plant. With a capacity of more than 700 megawatts, the electrolysis plant will be one of the largest of its type in Europe. The electrolysers required for this will be supplied by thyssenkrupp nucera. The core of the plant will be the standardised 20-megawatt scalum® modules sourced from the Dortmund-based company. The scalum® modules will be interconnected, permitting capacities in the high megawatt or even gigawatt range.
Hydrogen instead of carbon monoxide as a reducing gas
H2 Green Steel will then use the hydrogen obtained as a reducing gas: iron ore is reduced to sponge iron at around 950° C by adding hydrogen in the direct reduced iron plant. This removes oxygen atoms and impurities from the iron ore and produces water as a by-product.
Further processing in the mini-mill steelworks
The sponge iron obtained has an iron content of 90 to 95% and can be pressed into briquettes (HBI = hot briquetted iron) and subsequently sold. However, it can also be fed directly from the reduction plant into the mini-mill steelworks which processes the sponge iron to form various types of flat steel.
H2 Green Steel ordered from SMS group GmbH all the equipment for the construction of the mini-mill steelworks. Under the project, the Düsseldorf-based company is supplying a hot rolling mill as well as a cold rolling and strip processing line complex for the production of a wide range of products. The company is also responsible for overseeing the installation.
Low carbon emissions
Iron reduction is the most emission-intensive process step in conventional steel production, as the reducing gas used is carbon monoxide, which has hitherto been derived from natural gas. Carbon dioxide is produced as a by-product during the reduction process. Using alkaline water electrolysis technology to produce green hydrogen, H2 Green Steel can cut carbon emissions by up to 95 per cent to almost zero. This reduction in greenhouse gases can make a significant contribution to decarbonising steel production and the processing sectors.
Reduced carbon footprint
Investors in the steelworks in the Swedish Arctic Circle also include customers from various segments, such as the automotive industry, the commercial vehicle sector, the furniture industry and the industrial plant segment. Leading European car manufacturers have already signed agreements with H2 Green Steel for deliveries of green strip steel. In this way, they can significantly reduce their carbon footprint.
Photos: ©thyssenkrupp nucera, Dortmund, and H2 Green Steel, Stockholm (above)
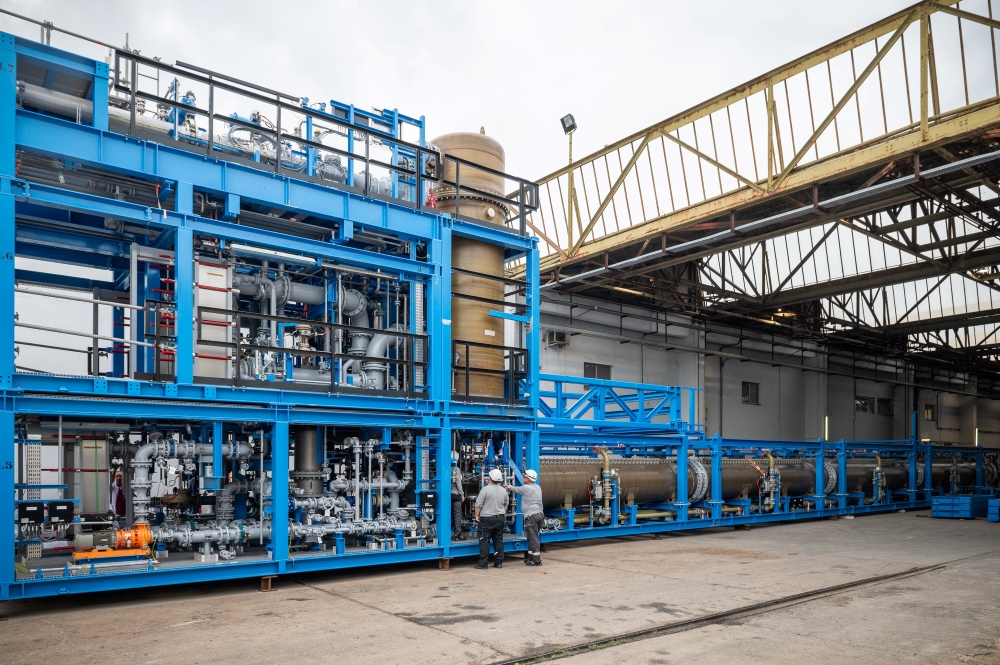
Backed by export credit guarantees
The German federal government will support the project by issuing export credit guarantees. It is providing manufacturing risk cover and supplier credit cover as well as contract bond cover and buyer credit cover.
“We are proud to be able to make a decisive contribution to the decarbonisation of the German export industry and its buyer countries with our export credit guarantees,” says Edna Schöne, a member of the Board of Management of Euler Hermes Kreditversicherungs-AG. “By backing exports, we are supporting the development of the latest and most innovative technologies from Germany, which will be used in the world’s first climate-neutral steelworks,” she adds.
Back to project overview